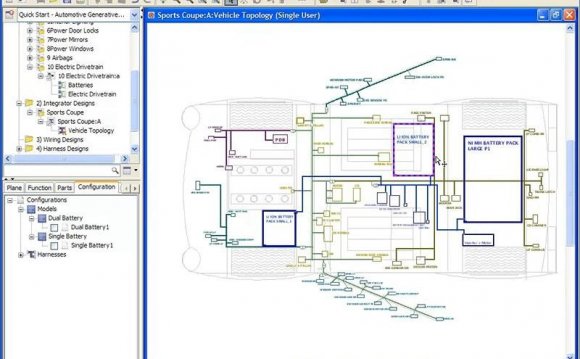
Electric and hybrid vehicles pose particular design challenges beyond those of conventionally powered vehicles. The electrical / electronic content is substantially higher and is more important in the overall cost picture. Novel electrical architectures with no previous industrial track record bring new risks and demand thorough evaluation in a virtual testing environment before release to the market.
Join Mentor Graphics for this session to learn how companies are improving their electrical vehicle design process by optimization of physical layout, modeling of battery charge / discharge, identification of safety issues and reduction of electromagnetic effects.
What You Will Learn
- How electrical designs can be analyzed for cable and component sizing using drive cycle simulation
- How electrical designs can be validated using failure modes effects analysis to eliminate the danger of hidden design errors
- How EMI effects can be minimized using automated cable routing
- How component layout can be optimized for cost and weight distribution
Phil Davies
Phil Davies, is a Product Manager at Mentor Graphics Integrated Electrical Systems Division (IESD). He worked for 11 years with BAR and Honda F1 Racing Teams where he was Electronics Design Manager and has 15 years experience in the application of electronics and electrical systems. His experience includes a wide range of MCAD and ECAD tools including the use and deployment of CATIA V5 & Enovia, Siemens NX & Teamcentre, SAP and VeSys Classic.
Who Should View
- Engineering management from OEMs and Systems Suppliers involved in electric and hybrid vehicle design
RELATED VIDEO
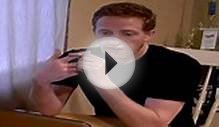
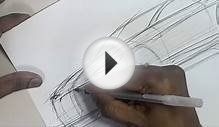
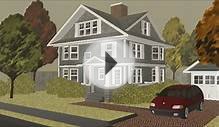