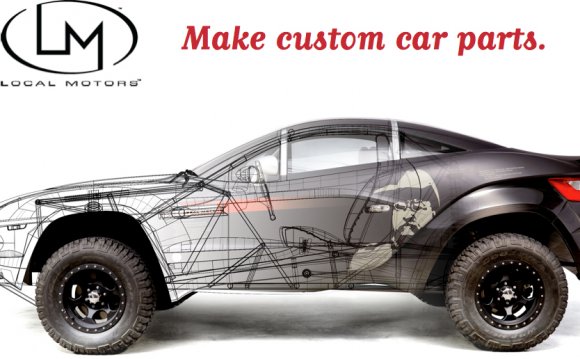
How do you produce a lightweight car seat prototype with a minimal volume and an optimal heat capacity? And how do you edit and 3D print such a large and complex file? Materialise has a solid reputation in the automotive industry, built on extensive knowledge in the production of large prototypes. In a quest to assist Toyota in creating a lightweight car seat, the software team added new features to our design enhancement software 3-maticSTL, and developed a slice-based operations technology which is incorporated into the Build Processor software.
To obtain an optimal design, it is often useful to take a peek at nature. Ages of evolution have formed optimized structures that offer valuable solutions for present-day issues in design and engineering. Toyota’s car seat design was inspired by bone structure, resulting in a gradient topology optimization with high-density and low-density areas, designed with the Materialise software Mimics. The design was then perfected and provided with a pattern in 3-maticSTL, and oriented on the build platform with Magics.
We now have an optimal design, but the main challenge is yet to come. Getting it printed! Complex designs, with lightweight structures, patterns or textures result in extremely large files that are hard to handle. With the slice-based operations technology of the Build Processor, the car seat’s file size could be reduced significantly and building it was a piece of cake.
RELATED VIDEO
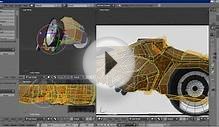
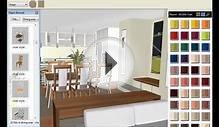
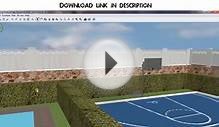