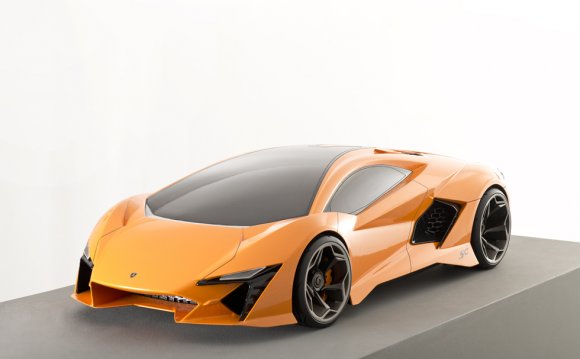
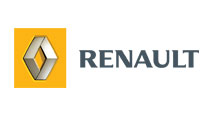
What the Industry Needs
Reverse engineering is a process by which the design of a product is analysed or re-created using a physical part or mock-up as a starting point. This becomes truly valuable when trying to extract the design intent from a handmade model (like a supercar), from discontinued parts or from an old design that was made without a 3D model reference (rare models, prototypes). The main goal here would be to create a 3D model that will match the functional design of the model (in this case mostly the visual and the aerodynamics). The critical steps in reverse engineering are acquiring, accurately and effi ciently, the shapes of the car body (mostly freeform) and extracting the information from the resulting scan in order to recreate the model as it is intended to be: a perfect CAD fi le that would be rid of the imperfections of the initial body.
Advantages of the HandySCAN 3D Solution
Reverse engineering calls for the acquisition of dimensions on parts of various shapes and complexity, potentially performed in any kind of environment. Due to its impressive portability, the HandySCAN 3D can perform the acquisition directly in the design studio but also on the customer's site, on a production floor or even in a small car body shop.
Since the designer wants to recreate the functional design of the part, the acquisition must be accurate and give all the information needed to reproduce a new reference model for the part to be manufactured; i.e. to create the stamping dies, tooling, brackets, assembly drawings, etc. The HandySCAN 3D will provide complete and accurate mesh models.
The HandySCAN 3D solution helps save a considerable amount of time compared to traditional measurement methods. Dimensions that are necessary for the reverse engineering process are quickly measured and are made readily available so that the designer can perform the work.
RELATED VIDEO
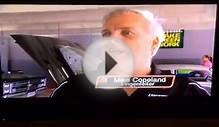
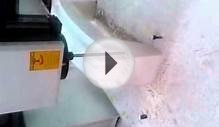
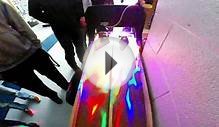